One of the things that often happens when office equipment leases come to an end, or when older equipment is being replaced, is a simplistic replacement process gets used. This can be a mistake if the time is not taken to step back and do a process review to ensure that the replacement optimizes the potential for business gains.
A recent project undertaken with an insurance group can illustrate how things can be changed, often with only minor differences but to effect a major benefit.
Client production scanning replacement scenario 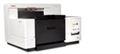
A client used high speed Kodak production scanners to capture paper records and transfer to another office for processing and filing. As part of the process the scanners had prescan imprinters installed to put a tiime/date stamp on the documents prior to the image capture. This imprint was part of the captured image and was used as a check process to ensure that all pages in a document were captured. The imprinters were an added option in the scanners, increasing their capital cost and had a running cost due to the need to replace ink cartridges for the imprinter. Given the high volumes being processed this was a fairly significant cost for the process.
The scanners were due for replacement and as the vendor we were asked to recommend suitable replacement models.
The easy thing to do would have been to simply look at the volumes, consider the current like for like replacement hardware and quote the price.
Process review leads to a revised way to do things
The need to have a time/date stamp on the document images was revisited and the client confirmed that this was a must have tool. As part of the process review questioning the timing of the stamp creation was raised. Did the time/date have to be attached prior to image creation or could it be added post or during image creation? After review the client determined that when it was created was not critical, just that it needed to be part of the process on a certifiable step in the defined work process.
There was discussion about a revised document pipeline in the future but for the purposes of the current application it was agreed that the critical needs were the time/date stamp and the new scanning equipment. The routing and handling of the images would remain as currently performed.
Investigation was undertaken to determine if a software based post image process could be put in place to eliminate the cost of the imprint options and the ongoing consumable costs of their operation. The result was the potential of a secured, post scan time/date stamp tool which attaches an improved stamp to each page as they are processed. This new software tool permits a post print digital imprint to be added to each scan image. It was determined that this process was no less secure than having a preprinted time/date stamp added. It may in fact prove more secure.
The potential for any alteration of images more specifically attaches to the potential for someone to try to manipulate the image created from the process. With the right software stamp this potential may be reduced although it might not be totally eliminated. In the end it was the decision of the client to implement the software solution and to save the capital costs and ongoing operating costs of the printed time/date stamp imprinter.
Further protection
One of the ways to further enhance the protection from electronic document tampering is to make sure that documents are stored in an electronic archive that itself includes security which deals with how documents are stored, checked out and modified. These types of systems offer rules around document access, handling and auditing for compliance and would make it far more difficult for anyone to download the file, edit it and re upload it un-noticed. They certainly beat Windows filing systems for such levels of security which too often is the default scanned image filing system used.
Process review a needed step in most office hardware replacements
No matter what type of office hardware you are replacing; production scanner, MFPs, computer systems or mailing systems a process review can be an important part of the replacement planning. Depending upon the size of the purchase and number of people or departments affected by the replacement even a smaller purchase can benefit from some review.
After all, tools, software and available methodologies are always changing. Very rapidly, given the shifts in office technologies. In the case above the software solution deployed had not been available at the time of the original scanner purchase.
Taking a few minutes or even some days to look at what the equipment is doing for you now and what it might need to be doing for you next year is time well spent. You too might be able to replace a step or steps in a current process in a manner to reduce your capital costs or operating costs or both. In doing so you might even be able to enhance other components of the system like security, user convenience or productivity.
Where has a process review brought you improvements? How hard was it?
Lee K